Services
Our customers come from the automotive and aviation industries as well as the power tools, home storage and other special applications for lithium-ion batteries.
Proteba location in Ulm, Germany
Proteba facilities
In our premises in Ulm we have at our disposal:
- Test bunker for battery abuse testing
- workshop
- Equipment for manufacturing of parts (CNC mill, 3D printer, etc.)
- laboratories, offices and conference rooms
- Machine hall for automated production of thermal barriers
We would be pleased to invite you for an initial consultation.
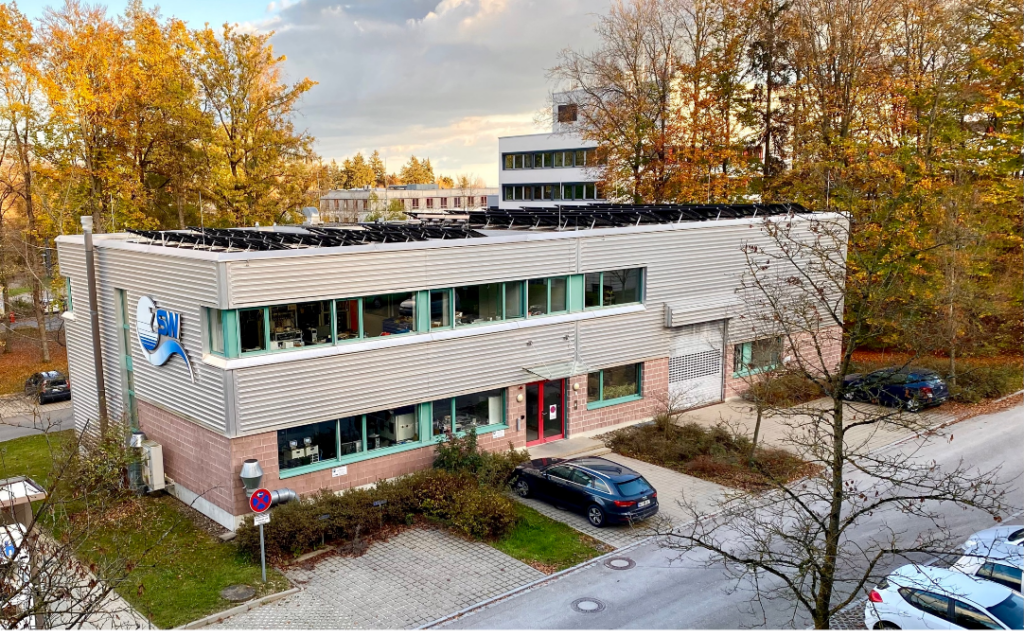
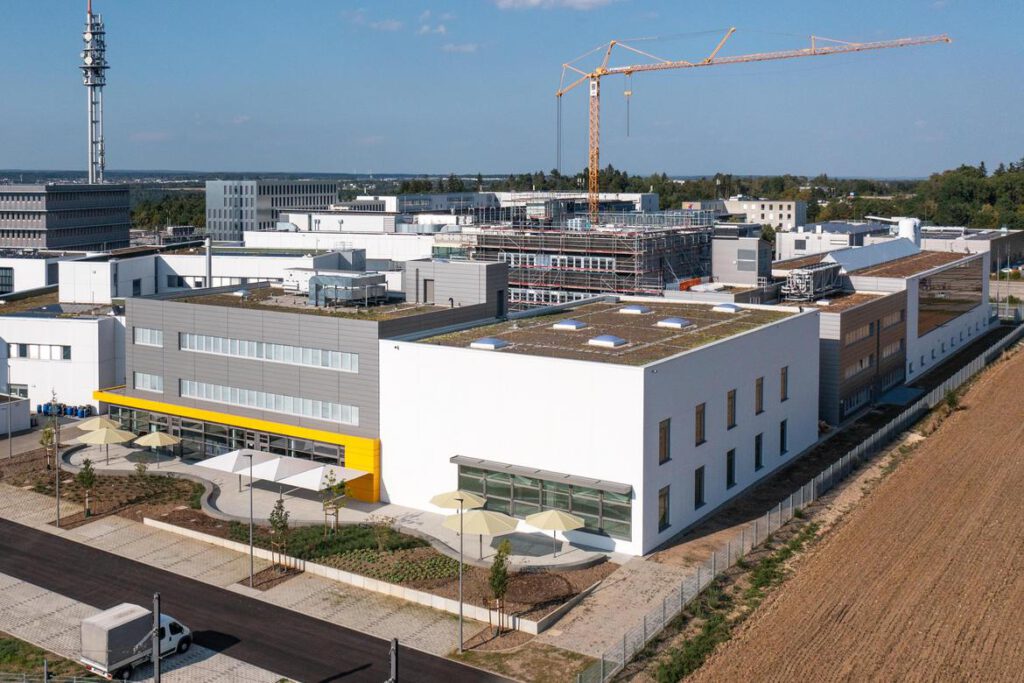
Connection to ZSW
Due to our founding history as a spin-off, we are closely linked to the Center for Solar Energy and Hydrogen Research Baden-Württemberg (ZSW) both geographically and at a working level. The ZSW has test field capacities in the battery sector for
- Electrical tests (Cell, Module, Pack)
- Safety testing
- Extensive analytics
- Cell opening and analyses
- Material research, lithium-Ion cell production and much more
Extensive construction work is currently underway to expand the Ulm site.
Test driven development approach
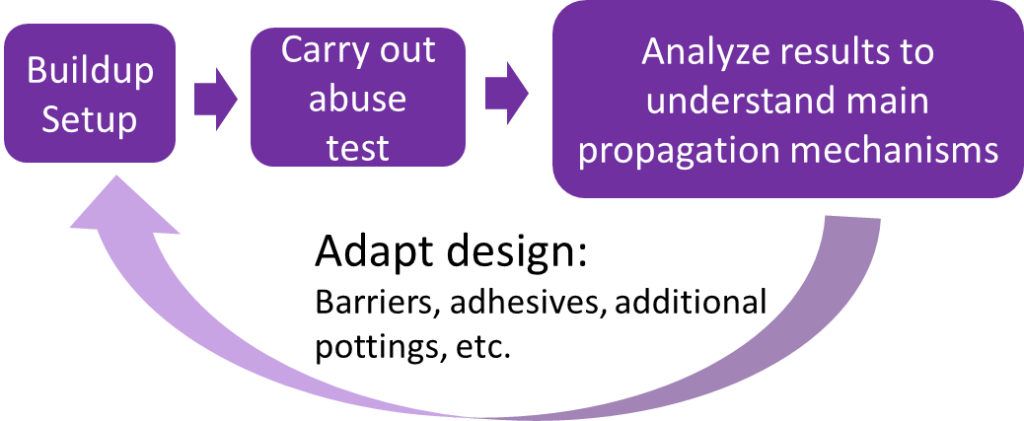
How can a battery development project be brought to a successful conclusion quickly and cost-effectively? How can nasty surprises be avoided in the TP test?
We believe that one part of the answer is a test-driven development approach. We validate our customers’ design drafts at an early stage of the development process by performing abuse tests on submodules. We are happy to use our rapid prototyping skills to support the build-up of test modules.
As part of the test series, we work with our customers to identify the optimum solution for all components that are important for preventing thermal propagation. We are also happy to advise on the use of Proteba products.
Measurement methods and characterization
We have extensive measuring equipment for a technically meaningful evaluation of thermal barriers, potting materials and other module components. Can we help you with the thermal characterization of battery modules and their components? Please send us a message.
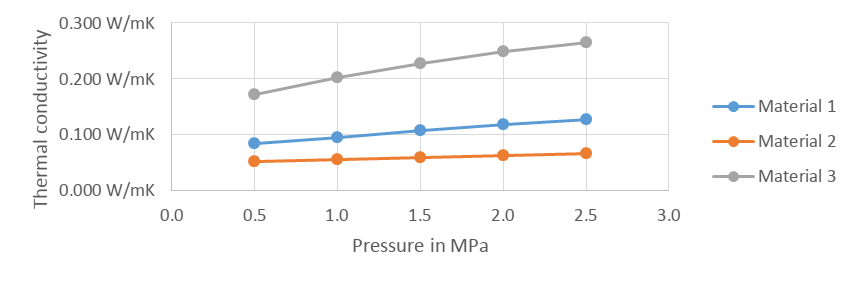
Thermal Conductivity
Thermal conductivity as a function of clamping pressure is a key factor in evaluating the performance of thermal barriers. Some example results of corresponding measurements on commercially available barrier materials are shown on the left.
Mechanical design
Thermal barriers are clamped between the individual cells under pressure. Due to reversible and irreversible expansion of the cells during charging and discharging as well as during ageing, the bracing pressure can increase significantly.
As safety-critical components, thermal barriers must be designed in such a way that the protective effect is ensured even under the highest pressure load.
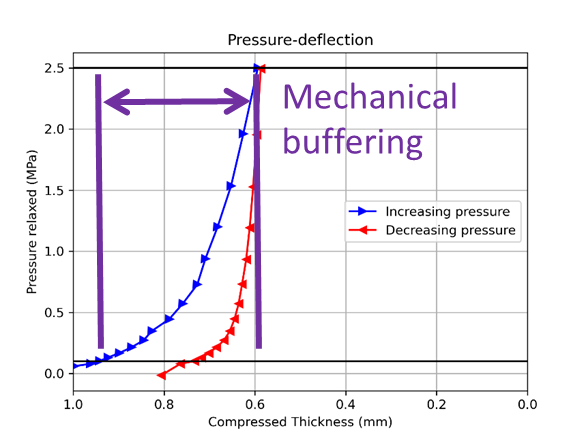
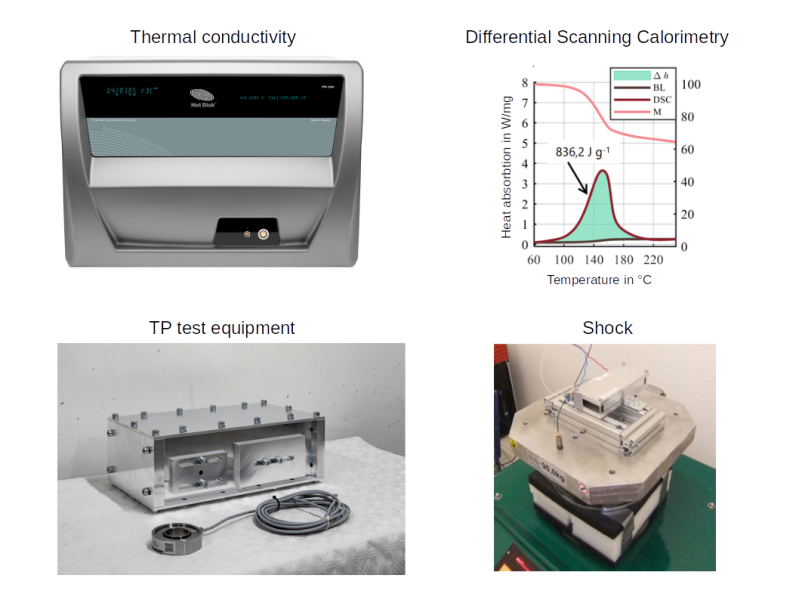
Other ParameterS
The development of battery modules is a complex task. A large number of design goals must be achieved and validated through experiments. We are happy to provide support (also in cooperation with ZSW, depending on the method):
- Electrical and thermal cycling tests
- Tailor-made test setups for abuse testing
- Force/deflection
- Thermal conductivity of probes under various conditions
- Thermal capacity measurement
- Differential scanning calorimetry (DSC) for characterizing heat absorbtion in phase change materials (PCM) and entdothermically reactive materials
- Vibration / mechanical shock testing
- and many more